Fast, safe, and mess-free— Concrete Network said it best with their glowing review of our Deco-Peel and Acryl-Pen products showcased at the and the World of Concrete Outdoor Demo. Scroll down or click the link below to find out all the ways this product duo can get your outdoor concrete surfaces shining in time for spring:
LINK: http://bit.ly/2x5Ih4v
NOX-CRETE WORLD OF CONCRETE PRODUCT SPOTLIGHT
Discover how Deco-Peel and Acryl-Pen can make your job faster and easier
By Sean Rand
At the 2020 World of Concrete in Las Vegas, we were introduced to two products from Nox-Crete. During their booth demonstration, we saw exactly how these products can help make your job, as a contractor, faster and easier. After the event we followed up with Marty O’Mara, Decorative Segment Manager, to learn a bit more about these products and their uses.
Deco-Peel: Acrylic Sealer Removal System
If you’ve used old bed sheets to contain the stripping solution when removing sealer, or even avoided jobs because stripping multiple layers of sealer seems like a hassle, then Deco-Peel* can help.
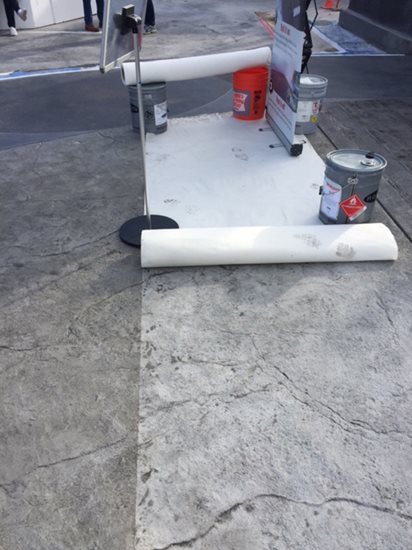
The Deco-Peel demonstration at World of Concrete.
It’s a blanket system that uses an engineered fabric paired with environmentally-friendly solvents. The system comes with 400 square feet of blanket and a 5-gallon pail of biodegradable stripper that you can apply with a roller.
Here is what makes Deco-Peel unique:
It’s Fast — After rolling out the blankets and saturating them with stripping solution, you’ll need approximately 2-4 hours, depending on weather, to complete the process.
It’s Safe — Deco-Peel doesn't contain any suspected cancer causing or aromatic solvents, such as methylene chloride, xylene or toluene. There are two versions to meet all state and federal VOC regulations.
It’s Mess Free — No pressure washer needed! When you’re done, simply peel off the blankets and dispose, without creating harmful waste.
Tips: “If you aren’t sure how many layers of sealer you’re dealing with, we offer a free test kit, which comes with a small 2’ x 2’ blanket and container of stripper,” Marty shares (contact Nox-Crete for details, see below). "Also, the best time to apply Deco-Peel is in the early morning or late afternoon when the sun is low. This avoids the solvents flashing too quickly and not doing their job," he adds.
Acryl-Pen: 3-in-1 Stain and Sealer
The second product that caught our eye at the show was Acryl-Pen*. It’s a penetrating water-repellent sealer and stain for exterior, horizontal concrete.

An Acryl-Pen driveway in Seattle still looking good after seven years.
Here are three reasons you might want to give it a try:
It’s a time saver
Acryl-Pen can help speed up your turnaround time because:
• You won’t have to apply multiple products
• It’s easy to apply, and only takes 2 coats
• Your project will be ready for traffic in 72 hours
• It has a long life span
Acryl-Pen has a reputation for being especially long lasting, here’s why:
• It penetrates the pores of the concrete deeply
• It prevents freeze/thaw damage and is breathable
• It’s UV resistant and won’t fade, chalk or flake
“It was used in Seattle on a driveway, and after seven years of Pacific Northwest rain, still looked great,” Marty recalls.
It offers lots of color choice
•Acryl-Pen is great for enlivening outdoor concrete with brilliant color.
• It’s available in 11 standard colors
• Multiple colors can be used together for producing creative designs
• Custom colors can be created through color matching
“At Boise State University it was used on the player's walkout area in the football stadium, where we matched their iconic blue astro turf,” says Marty.
Tip: “When integral color concrete is specified, the owner and architects expect it to be consistent throughout. It doesn’t happen often, but when the concrete is placed and it’s not consistent, Acryl-Pen will deliver long-lasting and consistent color,” Marty explains.
*Read and follow all application and precaution guidelines before applying these products.